MagMatrix -- The Newest Generation MgO Board MFG with Basic Magnesium Sulfate Cementitous Formula
- JP Group MagMatrix Brand
- Jun 4, 2021
- 4 min read
MagMatrix -- The Newest Generation MgO Board MFG with Basic Magnesium Sulfate Cementitous Formula -- Applied for Fire Rated Structural Board to Replace Portland Cement Board & Plywood & Osb Wood Panels
Research on technology of performance improvement of basic magnesium sulfate cementitious formula --Newest Chloride Free MgO Board Formula
MagMatrix is using and upgrading this BMSC formula of green building board for the MgO board industry. Basic magnesium sulfate cementitious formula for MgO board industry is a new type of magnesium cementitious materials, which has similar advantages with magnesium oxychloride cementitious materials, such as lightweight, fast setting, high strength, wear resistance, and is not easy to absorb moisture. It can widely replace magnesium oxychloride cementitious formula in the field of building insulation materials. In addition, the BMSC formula has 2.5 times the flexural strength of Portland cement of the same strength grade, and its durability and reinforcement protection performance are similar to Portland cementitious board, which also has a good application prospect in the field of civil engineering.
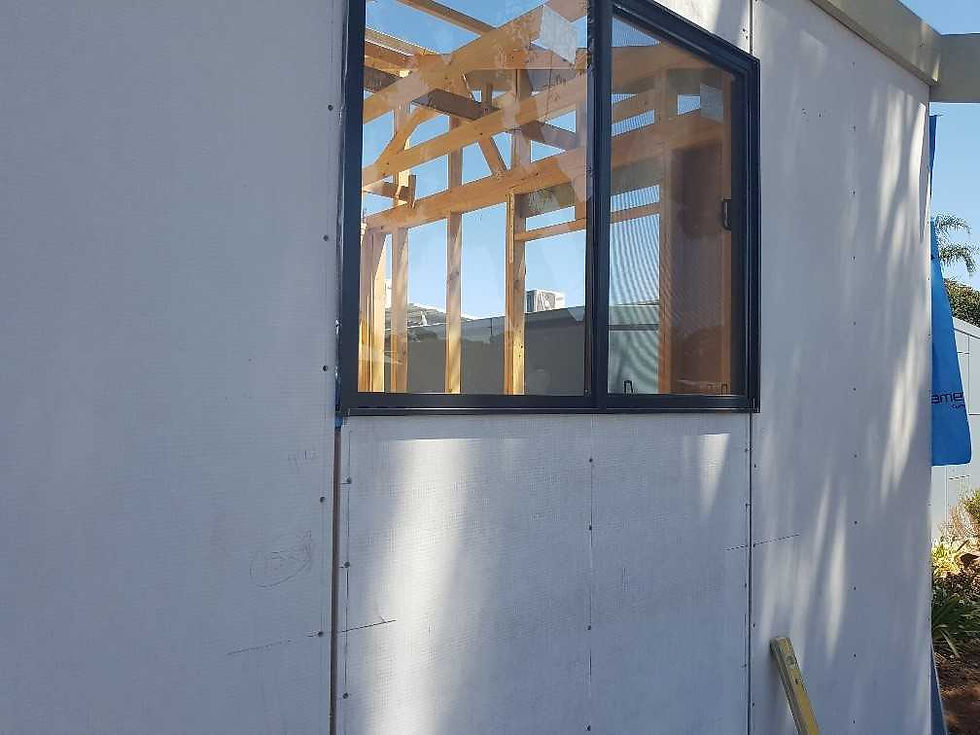
Basic magnesium sulfate cementitious board is a new type of magnesium cementitious material with the core of admixture technology. It is mainly made up of light burned magnesia, magnesium sulfate, a mineral admixture of different crystal water, and chemical admixture. It is used in the same way as ordinary Portland Cement. The solubility of its main hydration product 5Mg (OH)2-MgSO4-7H2O phase (517) is only 0.034g/100g water, which is basically the same as Portland cement, much lower than magnesium oxychloride cement, which can widely replace magnesium oxychloride cementitious panels in the field of building insulation materials. Besides, the MagMatrix BSMC formula MgO board has large rigidity, good seismic performance, and its bending, tensile and impact resistance performance are better than of the Portland cementitious concrete at the same grade, which also has a good application prospect in the field of structural engineering in building industry, also, of on the passive fire protection industry, too. In structural building systems, more importantly, the calcination temperature of light burned magnesia used to prepare BMSC is low, which makes BMSC friendly cementitious board in the future with great development potential.
Introduction of 517 Phase
Basic magnesium sulfate cementitious board (BMS) is a new type of Magnesium Cementitous material, which is developed on the basis of the research of magnesium oxychloride cementitious (MOC) and magnesium oxysulfate cementitious (MOS). It is mainly a ternary gelling system of MgO-MgSO4-H2O formed by the reaction of the solution of magnesium sulfate, the light magnesium oxide, and the chemical admixtures. in 1867, French scholar S. Sorel invented a gas-hardening MOC made of light burned MgO and a certain concentration of MgCl2. This cement has the advantages of a lightweight, high strength, abrasion resistance, and good adhesion to the plant fibers, but also has disadvantages such as poor water resistance, easy absorption of moisture and halogen, whitening, and frost, warping and deformation, and corrosion of reinforcing steel. After that, MOS was made by using MgSO4 solution instead of the solution of MgCl2, which solved the problem of steel corrosion, moisture absorption, and halogenation of MOC, Nevertheless, only 3Mg(OH2)-MgSO4-8HO (318)in four oxysulfate products produced after setting and hardening are stable at 35 degrees. And 318 phase is not a stable phase at room temperature. As if the MOS was prepared with active MgO and MgSO4 or the solution of MgSO4 at room temperature, the content of the 3-1-8 phase in the hydration product would not exceed 50%. This leads to a lower intensity of MOS than that of MOC, which is also the main reason for the poor water resistance of MOS. After years of study and research, it has been found that the strength and durability of MOS can be greatly improved by the addition of chemical additives in the process of preparation of MOS. The hydration product of the new cementitious materials is a new type of needle and rod phase, namely 5Mg(OH2)-MgSO4-7H2O phase (5-1-7) which is different from the traditional MOC and MOS. In view of the low solubility and strength of this modified MOS hydration product of the new cementitious materials is far higher than that of traditional MOS, the new cementitious materials were named BMS.
Sheathing & Fire Protection
MagMatrix Group invested huge fund in the research and development of the new BMS formula in the green MgO board industry and set up a state-of-art plant to produce the most stable and quality reliable BMS Magnesium Oxide Board which is the ideal solution panels on the modular building systems and also the passive fire protection industry. We are applying certification of BBA for the UK market and also ETA for the EU market and CCRR from Intertek and ICC-ESR certification for the North America market to meet the ICC & IRC building code, especially for the ASTM E136 Noncombustible grade to upgrade our board into I & II building code to make totally noncombustible applications for fire-rated sheathing, lining, subfloor sheathing, passive fire protection board.

We are also carrying out the 12mm board for 2 hours FRL design with Certifire test and certification in the coming time. it is a green building material that will save about 70% more emissions than Portland cementitious board to product our planet and cut emissions. Also, get it as moisture protection as it will not deteriorate when subjected to water or moisture. It is mold resistant as it contains no cellulose thus is resilient to mold growth. It is also environmentally friendly as it does not contain silicates so it is better for the installer.MagMatrix boards provide exceptional performance compared to wood, gypsum, and Portland cement-based boards. It is extremely strong with great impact resistance. It is fire-rated and suits a number of finishes. It is a natural product, environmentally friendly, and breathable. As it is BMS-based, homogeneous, environmentally friendly with a manufacturing process that produces very little in the way of CO2 emissions, unlike cement particle and gypsum boards which both generate high levels of CO2 emissions. Our board help provides a safe and healthy living environment whilst being a great surface to tile onto. Warm welcome your nice inquiry and to seek potential business partner on this new but excellent green building board.
David.Zhao@MagMatrixBoards.com
Please examine the following document:
https://assets.ctfassets.net/rg5y8r6t6cjr/2wgWmldViyznB5XrAX9Qg5/bebca3bfe360d64b33662ab105bc3f3f/Towards_Greener_sheets.pdf
On Page 06 - Table 2 Your will see under CO2 Air Emissions, for 6mm Villaboard lining 11.9 Kg of CO2 is emitted per square metre of product.
What is an exact and provable equivalent to this figure for your product.
This is important. Please don't delay in providing me with an answer.
Many thanks,
David Wheeler