MagMatrix Magnesium Oxide Board Exterior Rendering System
- JP Group MagMatrix Brand
- Nov 21, 2024
- 4 min read
Learn more about rendering exterior walls
Rendering exterior walls is the process of applying external wall coverings with render to protect the blocks or bricks from which the building is constructed. Usually, it is covered with a thin coat of paint or any wall coating to protect the render surface from erosion or cracks.
You need good maintenance of the wall covering if the exterior walls of your building are rendered to prevent instances of water ingress and penetration of dampness through the render finish into the house.
Render can be sand and cement render scratch coat or a more breathable, flexible polymer render for houses with solid walls, or other suitable materials such as lime render, acrylic render, monocouche render, silicone render, and mineral render.
It helps to hide mismatched brickwork or poor-quality period properties and creates a uniform finish on contemporary homes. It can be painted later or comes already self-colored. Render works well with timber cladding or external masonry paint to add architectural interest.
Also, you can match it with external wall insulation to improve energy efficiency and save long-term heating costs.
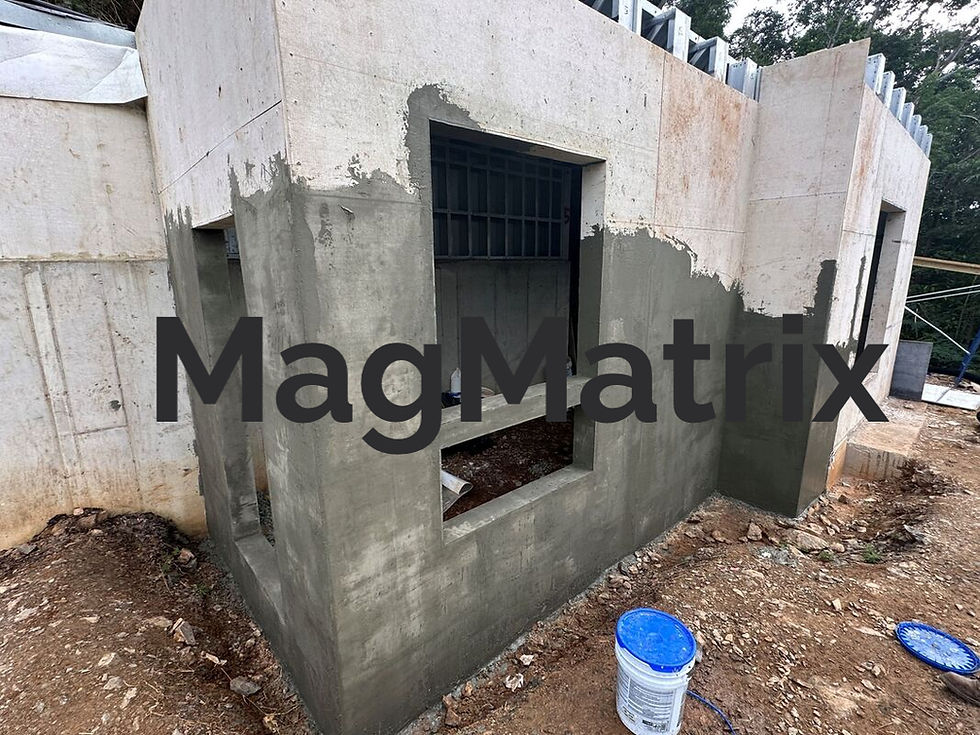
Purpose of Rendering
Protection: Shields the underlying brick or blockwork from weathering, erosion, and water ingress. Acts as a barrier against damp penetration into the interior.
Aesthetic Enhancement: Provides a smooth or textured finish, hiding imperfections like mismatched bricks or outdated materials. Offers a wide range of finishes to suit modern and traditional architectural styles.
Energy Efficiency: It can be paired with external wall insulation (EWI) to improve thermal performance and reduce heating and cooling costs.
Benefits of Rendering
Weatherproofing: Protects walls from wind, rain, and frost damage.
Enhanced Durability: Extends the lifespan of the building's exterior.
Improved Curb Appeal: Creates a clean, polished look.
Cost-Effective Insulation: Combining with EWI reduces energy bills over time.
Magnesium Oxide Board Exterior Rendering System
An exterior Magnesium Oxide (MgO) board rendering system uses MgO boards as a substrate for exterior wall cladding or rendering. This system is increasingly popular due to MgO's durability, fire resistance, and resistance to water, mold, and insects. Below is an overview of how MgO boards are used in exterior rendering systems.
Key Features of a MgO Exterior Rendering System
Durable Substrate: MgO boards provide a robust base for render applications, offering superior structural support compared to traditional materials like plywood or gypsum.
Weather Resistance: MgO boards are highly resistant to moisture, preventing deterioration due to weather exposure.
Fire Resistance: Class A fire-rated boards enhance the safety of the building envelope.
Versatile Finishes: Compatible with various rendering finishes, including acrylic, cementitious, and lime-based renders.
Eco-Friendly: MgO boards are a sustainable alternative with a lower carbon footprint and no toxic additives.
Components of a Magnesium Oxide Board Exterior Rendering System
MgO Board: Acts as the primary sheathing. Installed directly onto the framing system or over an insulation layer.
Primer or Bonding Agent: Ensures good adhesion between the MgO board and the rendering material. Specialized primers are available for compatibility with MgO surfaces.
Base Coat: A cementitious layer is often applied over the MgO board. Reinforced with fiberglass mesh to prevent cracking and improve impact resistance.
Fiberglass Mesh: Embedded into the base coat to enhance flexibility and strength.
Rendering Material: Final finish layer, customized for texture and color.
Options include:
Acrylic Render: Flexible and resistant to cracking.
Cement Render: Durable and cost-effective.
Lime Render: Breathable and traditional.
Silicone Render: Hydrophobic and self-cleaning.
Sealer: Applied as the final layer to protect the render from UV rays, moisture, and stains.
Installation Steps
Preparation: Ensure the MgO board is securely fastened to the framing with corrosion-resistant screws. Seal joints with an approved jointing compound and tape to create a smooth surface.
Primer Application: To enhance adhesion, apply a primer to the MgO board surface.
Base Coat and Mesh: Spread the base coat evenly over the board. Embed the fiberglass mesh into the wet base coat, ensuring overlaps at mesh seams.
Rendering Application: Once the base coat cures, apply the render in layers according to manufacturer instructions. Use trowels or spray systems to achieve the desired finish.
Sealing: Apply a protective sealer to extend the lifespan of the render.
Benefits of a Magnesium Oxide Board Exterior Rendering System
Enhanced Durability: Resistant to cracking, weathering, and environmental stress.
Low Maintenance: Requires minimal upkeep compared to traditional systems.
Improved Energy Efficiency: Often combined with insulation layers for better thermal performance.
Sustainable Choice: Eco-friendly manufacturing process and recyclable material.
Design Considerations
Breathability: Ensure the rendering system maintains proper vapor permeability to avoid moisture buildup.
Expansion Joints: Install expansion joints to accommodate thermal movement in large wall areas.
Climatic Suitability: Choose render types appropriate for the local climate.
This system combines magnesium oxide boards' structural and protective qualities with a visually appealing exterior finish, making it an ideal solution for modern construction projects. MagMatrix, the BMSC 517 new sulfate magnesium oxide board of the fire-rated exterior structural sheathing panel, is an all-in-one exterior wall system that helps you get the fire-rated and shear wall ability in the single panel and might help improve the design for the exterior walls for fire ratings to use all deduct off the fire rated gypsum layers help you make cost savings and increase the exterior wall with the rendering system for quicker installations.
Comments