Comparison of MgO Panels Underlayment with Wet-Laid Gypsum Underlayment
- JP Group MagMatrix Brand
- Sep 19, 2024
- 5 min read
When comparing MgO panels with wet-laid gypsum underlayment, several critical differences in material properties, performance, and application emerge:
Fire Resistance
MgO Panels: Naturally fire-resistant due to their composition of magnesium oxide. They have a high fire rating and can withstand extreme temperatures, making them suitable for fire-rated assemblies. MgO boards typically achieve Class A fire ratings.
Wet-Laid Gypsum Underlayment: While gypsum also provides fire resistance, it generally requires additives and additional layers (such as Type X gypsum) to achieve comparable fire ratings to MgO panels. Gypsum boards are also non-combustible but do not perform as well under prolonged exposure to fire compared to MgO.
Water Resistance
MgO Panels are highly resistant to water and moisture, making them suitable for use in humid environments or areas prone to water exposure. MgO boards do not swell, mold, or degrade when exposed to moisture, and they maintain structural integrity over time.
Wet-Laid Gypsum Underlayment: Gypsum is more susceptible to water damage. When exposed to moisture for extended periods, wet-laid gypsum can soften, swell, or break down, leading to mold and mildew growth. Even water-resistant gypsum boards need added treatments to withstand moisture.
Structural Strength
MgO Panels: Known for superior flexural strength, impact resistance, and dimensional stability. MgO boards are robust, making them suitable for load-bearing walls, floors, and roofs. Their high impact resistance also makes them ideal for areas subject to physical stress or wear.
Wet-Laid Gypsum Underlayment: Generally weaker than MgO panels regarding flexural strength and impact resistance. Gypsum is more brittle and prone to cracking under force or structural stress, making it less durable in high-traffic or load-bearing applications.
Environmental Impact
MgO Panels: MgO boards have a relatively low carbon footprint and cleaner production processes. Magnesium oxide is a naturally abundant resource, and manufacturing involves fewer harmful emissions than gypsum production.
Wet-Laid Gypsum Underlayment: Gypsum mining and production have a higher environmental impact. The process emits more CO₂, and gypsum often contains fly ash and other byproducts, which can raise environmental concerns.
Installation and Workability
MgO Panels: Due to their lightweight nature and flexibility, installing MgO panels is straightforward, though handling dust when cutting requires proper protection. MgO panels can often eliminate the need for additional layers, reducing labor time.
Wet laid gypsum Underlayment is easier to cut and handle than MgO boards. However, multiple layers of gypsum may be required to meet specific structural or fire performance needs, increasing labor time and material costs.
Cost
MgO Panels are typically more expensive upfront due to their advanced properties and durability, but they can offer long-term savings by reducing the need for repairs, replacements, and additional layers in assemblies.
Wet-laid gypsum Underlayment is generally more affordable in terms of material cost. However, the need for extra layers and potential repairs due to water or impact damage can increase the overall cost over time.
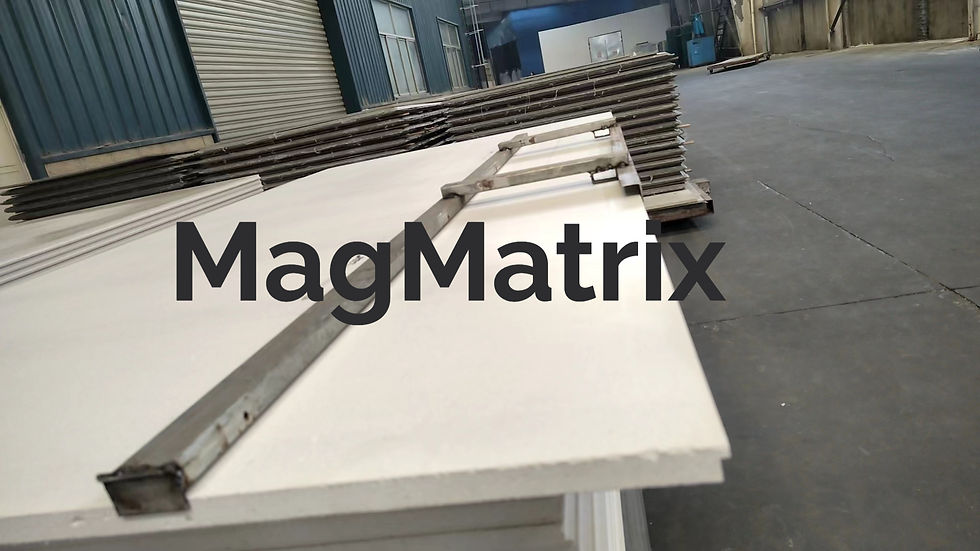

Wet-Laid Gypsum Underlayment
Wet-laid gypsum underlayments, particularly self-leveling varieties, are commonly used in construction to create a smooth, level subfloor ready for finishing. They have several key characteristics that differentiate them from other materials like MgO panels:
Critical Characteristics of Wet-Laid Gypsum Underlayments
Self-Leveling: Poured as a wet mixture, these underlayments settle into a level surface, minimizing manual labor for leveling. This is ideal for creating smooth surfaces over uneven subfloors.
Composition: It is made from gypsum or hydraulic cement, fillers, polymeric binders, and additives. The mixture's water content and additives control its flow, setting behavior, and strength.
On-Site Mixing: Typically mixed with water on-site, allowing for customizable installation based on specific job site conditions.
Fire Resistance: Some formulations can enhance fire resistance in assemblies, an essential consideration for multifamily or commercial projects.
Acoustic Properties: Gypsum underlayments can improve Sound Transmission Class (STC) and Impact Insulation Class (IIC) ratings, critical for reducing sound transmission in multifamily buildings.
Applications:
Subfloor Preparation: Wet-laid gypsum underlayments are mainly used to provide a smooth, level base for various floor coverings, such as tile, carpet, or hardwood.
Multifamily Construction: Their ability to improve fire and acoustic performance makes them attractive for multifamily housing where sound and fire code compliance are critical.
The use of wet-laid gypsum underlayments introduces several challenges to the construction process:
Moisture Introduction:
Excess Moisture in Wood-Framed Structures: The wet-laid application introduces a significant amount of moisture into the structure. If this moisture isn't controlled, it can become trapped in wood framing, leading to issues like:
Deformation: The wood may warp or swell due to excess moisture.
Deterioration: Prolonged moisture exposure can degrade the structural integrity of the wood.
Mold Growth: Moist environments promote mold growth, which poses health risks and affects the building's durability.
Impact on Construction Timeline:
Specialty Subcontractor Requirement: The need for a specialty crew to install the underlayment can complicate scheduling, as they need to work through different areas of the building after framing is completed and the building is protected from exterior weather.
Delayed Project Phases: Wet-laid underlayments require 5-7 days of curing under ideal conditions. During this time, no other work can be done on the floor, causing construction delays. Adverse conditions like high humidity, cold, or heat can extend curing times, further impacting the schedule and possibly adding expenses to maintain optimal temperatures for curing.
Partition Issues:
Doesn’t Extend Under Partitions: Wet-laid underlayment typically does not continue under framed partitions, which may compromise fire and acoustical resistance in those areas. If partitions need to be moved in the future, leveling the floor with the surrounding underlayment can be problematic.
These factors make planning and moisture management essential when using wet-laid gypsum underlayments, especially in wood-framed construction.

MgO panels as underlayment offer several advantages over traditional wet-laid gypsum underlayments:
Dry Installation Process:
No Water or Curing Required: MgO panels do not require water for installation, preventing excess moisture from entering wood framing. This also eliminates the need for controlled curing conditions, which can be time-consuming and costly in gypsum underlayments.
No Delays Due to Curing: Since no curing is necessary, construction projects can proceed without the typical 5-7 day delay required for gypsum underlayments to set and harden.
Simplified Construction:
Framers Can Install MgO Panels: MgO panel are installedl similarly to wood subflooring products using standard woodworking tools and fasteners. This allows framers on-site to handle the installation without requiring a separate specialty crew, reducing labor costs and simplifying the project workflow.
Installed Before Wall Framing: MgO underlayment can be installed before wall partitions are framed, creating a continuous subfloor layer. This ensures better fire and acoustic performance since there are no gaps where the underlayment doesn’t extend beneath partitions.
Acoustical and Fire Performance:
Continuous Layer: Unlike gypsum underlayments that don’t extend under partitions, MgO panels provide a seamless layer that enhances fire resistance and sound transmission control. This is especially beneficial in multifamily or commercial construction, where these properties are critical.
Customizable Assembly Option: Depending on performance needs, MgO panels can be paired with structural wood panels or sound mats to create specific acoustical or fire-rated assemblies. Manufacturers can discuss these variations during the design phase to optimize performance.
MgO panels provide a practical, time-efficient alternative to wet-laid gypsum underlayments by streamlining installation and avoiding moisture-related risks.
In conclusion, MgO panels present a highly effective and efficient alternative to conventional materials like wood-based panels and wet-laid gypsum underlayments in multifamily construction. Their dry installation prevents moisture-related issues, reduces project delays, and maintains essential fire and acoustic performance. When specifying MgO panels, selecting high-quality versions with engineered formulations and integrated mesh cores is crucial for optimal structural performance. MagMatrix BMSC 517 new sulfate MGO board for the underlayment models gives you an incredible fire resistance structurally dry conditions layout underlayment in the type IIIA multifamily constructions. This ensures that design professionals can achieve time efficiency and durability without compromising safety or building standards.
Comments